Written by Adam Dawson, Pryda’s ANZ Technical Manager, this article was published as an FTMA Tech Talk in May 2020.
Timber connection systems rely on a combination of the correct product, fasteners and installation practices to achieve their required capacity. They are typically designed and tested by the manufacturer using their proprietary nails or screws and may also be sold to the consumer with these fasteners included. In the case of nailed connections, the nails were originally all hand-hammered through precut holes to help ensure the correct interface between the timber and the connector.
The quality of the connection is highly dependent on how it is fastened to the timber, considering the type of nail, quantity of nails, nail spacing, proximity to the edges and holes in the connector and proximity to timber edges. With all these variables, it is essential that the installer is familiar with the product’s design guide and the correct nail placement, noting that there may be several different acceptable nailing patterns to achieve different capacities.
With advances in technology leading to tools that are increasingly safe, reliable and easy to use, nailing tools are now nearly ubiquitous on building sites and frequently used for installing brackets, bracing and other connections. They offer increased speed and can be as accurate as hand-nailing when used correctly. However, if faster nailing comes at the cost of correct nail placement, the consequences for the strength of the connection and the stability of the structure can be severe. Concerns about installation quality led to the Queensland Building and Construction Commission banning the use of machine-driven nails for tie down connections in 2015.
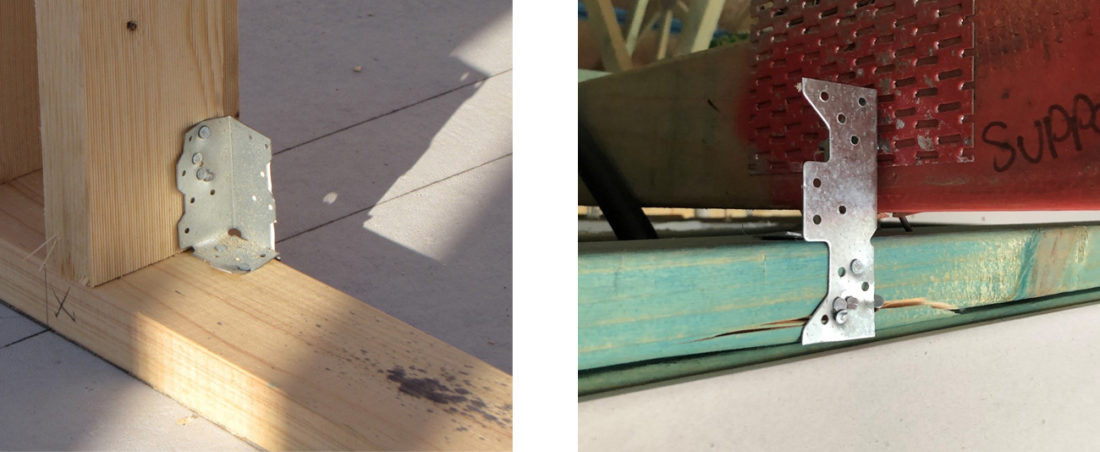
Nevertheless, nailing tools are the reality on most sites and the benefits are significant, potentially saving days of carpentry on a typical house. The motivation for builders to use machine-driven nails is obvious, and timber connector manufacturers have responded by highlighting the importance of accurate nailing in their technical literature. Data sheets and design guides for bracing and bracket connections address how to achieve a compliant connection with both hand-hammered and machine-driven nails, where possible, noting the restrictions in Queensland.
Manufacturers will typically specify that at least one additional nail is required when using a nailing tool versus hand-hammering, due to the smaller diameter of most machine-fired nails. When this is the case, machine-driven nails should be installed through the solid metal sections of the connector (also known as the blanks), with care taken to ensure they are located appropriately to meet the minimum edge distance and spacing requirements from AS1720 (below).
Where tools are available that can fire the correct nail diameter and can install these nails precisely in the holes, such as a positive placement nailer, they can be used to install connectors using the same quantity of nails as hand-hammering.
Given the reliance on the installer and the potential for errors, as clearly demonstrated in these photos, it is important that everyone in the industry is vigilant when it comes to these connections. Extra care must be taken during installation and inspections, particularly with critical connections such as tie-downs, to ensure the connection achieves the capacity it was designed for.
Frame and truss fabricators can be justifiably alarmed at the potential for their products to be insufficiently connected and tied down. They are also well-placed in the construction process to influence positive changes through the way they supply connection systems. The product landscape is changing to address these challenges and there may be better alternatives. As an industry we should all be thinking about the time, cost, compliance and safety features of the whole system – connector, fastener and tool – and promoting solutions that give certifiers and homeowners confidence that homes are compliant and built to last.